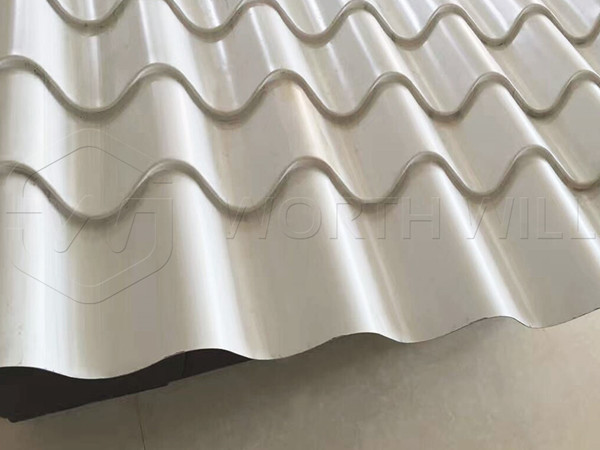
Key Considerations When Choosing Aluminium Corrugated Sheets
Aluminum corrugated sheets are widely used in various construction, industrial, and roofing applications due to their durability, lightweight nature, and resistance to corrosion. Whether you’re planning a roofing project, cladding, or even creating decorative elements, aluminium corrugated sheets offer a range of benefits. However, to make the most out of this material, it’s crucial to consider several factors before making a purchase.
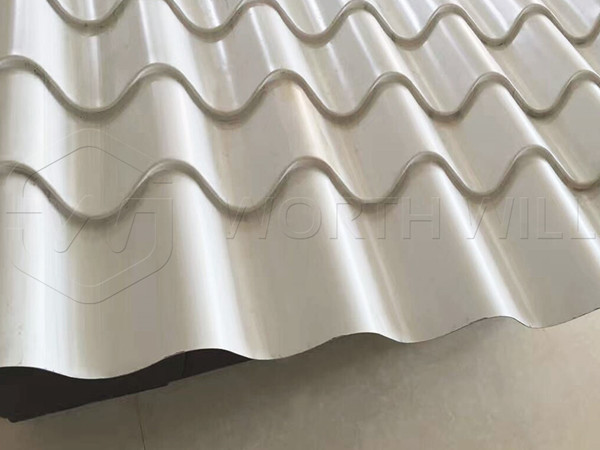
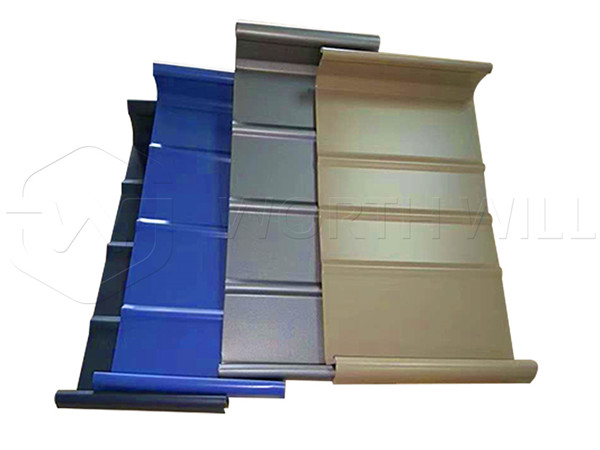
1. Thickness and Gauge
The thickness of the aluminium corrugated sheet is one of the first factors to consider. The thickness, often referred to as the gauge, directly impacts the sheet’s strength, durability, and overall performance. Thicker sheets provide better structural integrity and are suitable for heavy-duty applications, such as industrial roofing or large-scale construction projects. However, for applications where weight savings and flexibility are more important, thinner sheets might be a better choice.
- Common Thicknesses: Aluminum corrugated sheets typically range from 0.2 mm to 1.2 mm in thickness.
- Application-Specific Gauges: Thicker sheets are often used for roofing and structural work, while thinner sheets are ideal for decorative purposes or lightweight cladding.
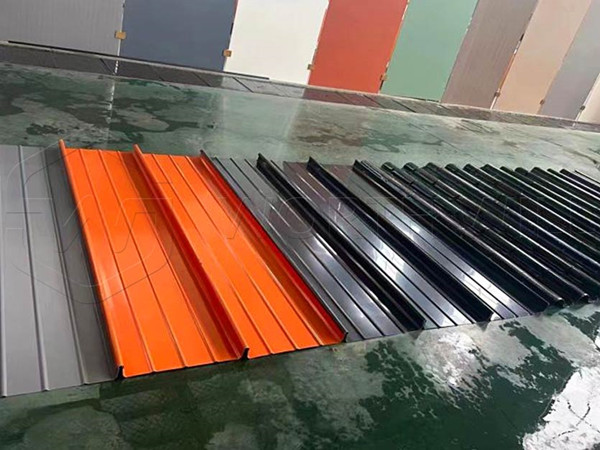
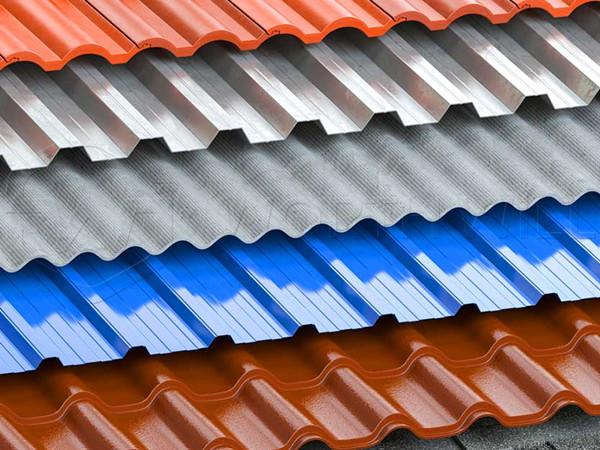
2. Profile Design
Aluminium corrugated sheets come in various profiles, each with a specific design and use case. The profile refers to the pattern of ridges and valleys (or “corrugations”) that run along the length of the sheet. The choice of profile affects not only the aesthetic appeal of the sheet but also its structural performance.
- Wave Profiles: Wave-like corrugations are the most common, providing a traditional look and excellent drainage capabilities for roofing.
- Trapezoidal Profiles: Trapezoidal or box profiles offer enhanced strength and are often used in load-bearing applications like industrial roofing.
- Custom Profiles: Some manufacturers offer custom profiles for specific aesthetic or functional needs. If your project has unique requirements, consider discussing custom options with your supplier.
3. Alloy Composition
Aluminium corrugated sheets are made from different aluminum alloys, each offering specific properties. The choice of alloy can impact factors such as corrosion resistance, strength, and flexibility.
- 3000 Series: This series is known for its good corrosion resistance and moderate strength, making it ideal for general construction and roofing.
- 5000 Series: Offering higher strength and better corrosion resistance, especially in marine environments, this series is suitable for demanding applications.
- 6000 Series: These alloys are known for their excellent strength and versatility, making them suitable for structural applications.
When choosing an aluminium corrugated sheet, ensure that the alloy composition matches the environmental conditions and structural demands of your project.
4. Coating and Finishing
Aluminium corrugated sheets are often coated or finished to enhance their durability, appearance, and performance. The type of coating can influence the sheet’s resistance to weather, UV rays, and corrosion.
- Anodized Finish: Anodizing adds a protective oxide layer, increasing the sheet’s resistance to corrosion and wear while also allowing for a variety of color options.
- Polyester Coating: A popular choice for roofing and cladding, polyester coatings provide good UV resistance and color retention.
- PVDF Coating: Polyvinylidene fluoride (PVDF) coatings offer excellent resistance to weathering and chemical exposure, making them suitable for harsh environments.
- Mill Finish: If aesthetics are not a priority and cost savings are essential, mill finish aluminum offers a raw, uncoated surface.
Consider the environmental conditions your project will face, such as exposure to saltwater, chemicals, or extreme temperatures, and choose a coating that offers the necessary protection.
5. Size and Dimensions
Aluminium corrugated sheets are available in various sizes and dimensions to accommodate different projects. Standard sizes are typically available, but many suppliers offer custom dimensions as well.
- Length: Standard lengths range from 6 feet to 12 feet, but custom lengths can be ordered based on your project needs.
- Width: Typical widths are between 26 inches and 48 inches.
- Custom Sizes: If your project requires specific dimensions, inquire about custom sizing options from your supplier.
Ensure the dimensions you choose are compatible with your project requirements to minimize waste and ensure a smooth installation process.
6. Weight and Transport Considerations
One of the advantages of aluminium corrugated sheets is their lightweight nature compared to other materials like steel. However, it’s still important to consider the weight, especially if you’re ordering in bulk or for a large-scale project. Lighter sheets are easier to handle and transport, reducing labor costs and installation time.
- Transportation: If you’re purchasing large quantities, consider how the sheets will be transported to your site. Choose a supplier who can handle the logistics or offers convenient delivery options.
- Handling: Lightweight sheets are easier to work with, but make sure they are handled properly to avoid damage during installation.
7. Installation and Maintenance
Aluminium corrugated sheets are known for their ease of installation, but it’s essential to consider the specific installation requirements of your project. For instance, ensure that the sheets are compatible with your roofing or cladding system and that you have the necessary tools and fasteners for installation.
- Installation Process: Aluminum corrugated sheets can be installed using screws, clips, or adhesive systems. Choose the method that best suits your project and the type of sheet you’re using.
- Maintenance Needs: One of the benefits of aluminum is its low maintenance requirements. However, periodic cleaning and inspections are recommended to maintain the sheet’s appearance and performance, especially in harsh environments.
8. Cost and Budget
While aluminium corrugated sheets are generally more affordable than other metal options, prices can vary based on factors like thickness, coating, and size. Consider your budget carefully and compare prices from different suppliers to get the best deal.
- Material Costs: Thicker and coated sheets tend to be more expensive, so balance your needs with your budget.
- Installation Costs: Factor in the cost of labor and any additional materials or tools required for installation.
- Long-Term Savings: Remember that investing in high-quality aluminum sheets with appropriate coatings can save you money in the long run by reducing maintenance and replacement costs.
9. Supplier Reputation and Service
Finally, choosing the right supplier is crucial. A reputable supplier will not only provide high-quality materials but also offer valuable advice and support throughout your project.
- Reputation: Look for suppliers with positive reviews and a track record of delivering high-quality aluminum corrugated sheets.
- Customer Service: Choose a supplier who is responsive and willing to assist with any questions or concerns you may have.
- After-Sales Support: Consider whether the supplier offers after-sales support, such as guidance on installation, maintenance, or warranties.
Conclusion
Choosing the right aluminum corrugated sheet involves balancing several factors, from material thickness and profile design to coating options and budget considerations. By taking the time to assess your project’s specific needs and working with a trusted supplier, you can ensure that your aluminum corrugated sheets will perform well and last for years to come.
If you’re ready to start your project or need expert advice, contact us today! We offer a wide range of aluminum corrugated sheets to suit any application, and our team is here to help you make the best choice for your needs.